01.不锈钢产品的种类
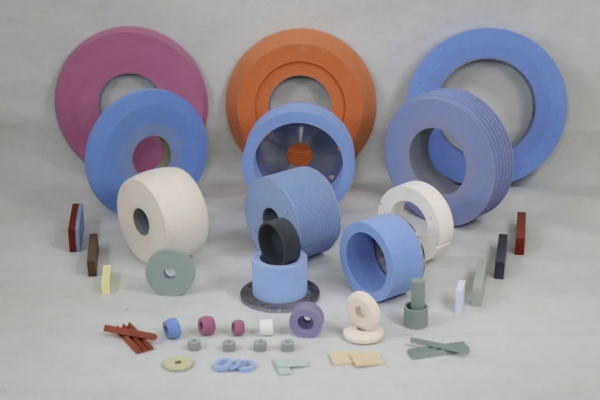
不锈钢的种类很多,按成分可分为铬不锈钢、铬镍不锈钢等,按内部组织可分为马氏体不锈钢、铁素体不锈钢、奥氏体不锈钢、奥氏体-铁素体不锈钢、沉淀硬化不锈钢等。
02.不锈钢的磨削特点
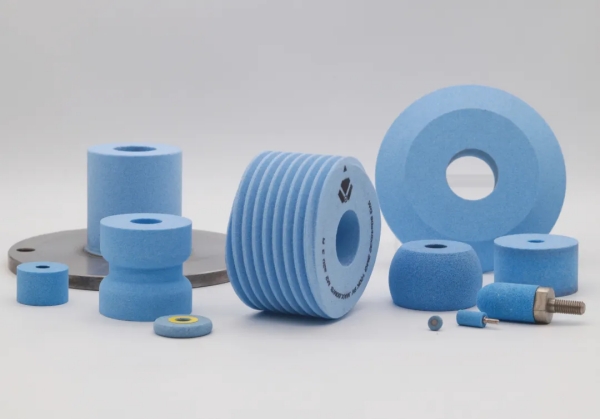
●磨削力大、磨削温度高
不锈钢材料具有高温、高强度、高韧性的特点,磨削时晶格畸变大、塑性变形剧烈,不锈钢单位面积的切削力可达90GPa,磨削力是45#钢的1.5-2.2倍,磨削阻力大,磨削区温度高。
不锈钢的导热系数较低,约为45#钢的1/3,使工件表面瞬间产生1000-1500℃的高温,工件表面易被烧伤,工件产生裂纹,有时工件表面产生退火,退火深度可达0.01-0.02mm。
●严重的加工硬化趋势
不锈钢磨削时,工件表面变形严重,应力应变增大,产生加工硬化,在加工硬化层中,晶粒发生畸变,砂粒磨损钝化,产生振痕、划痕。
●磨屑粘附在砂轮上
由于不锈钢的韧性很大,在一定的磨削温度、接触压力和相对速度条件下,磨屑很容易与砂粒发生反应,因此磨屑粘附在砂轮上,填满磨粒间的缝隙,使砂轮急剧堵塞。此时磨削条件迅速恶化,发热严重,表面粗糙度明显下降。
磨屑的粘附情况因不锈钢不同而不同,耐浓硝酸不锈钢和耐热不锈钢磨削粘附最严重,其次是1Cr18Ni9Ti、1Cr13、2Cr13等。
●磨屑不易切断,磨粒易磨钝
不锈钢材料磨削时,磨削力大,磨粒易磨钝,使砂轮磨损。一般不锈钢磨削时,磨削比为G=6-12,而普通碳钢和低合金钢磨削时,磨削比为G=40-80。因此,不锈钢的磨削比仅为普通钢的1/7左右。
●工件表面烧伤
工件表面烧伤是磨削加工中常见的缺陷之一,特别是奥氏体不锈钢,对烧伤更为敏感。
●工件表面划伤
不锈钢材料磨削时,工件表面易划伤,因此对已加工表面粗糙度要求较高。
划伤产生的原因:砂轮工作面上有个别突出的磨粒,在脱落前划伤了工件表面。从砂轮上脱落的磨屑落在砂轮与工件之间,造成工件表面划伤。磨屑液不干净,混有磨屑,磨屑液供应不足,磨削过程中产生划伤。
●工件变形
由于不锈钢的线膨胀系数较大,磨削温度对工件尺寸影响也较大,容易引起尺寸测量的误差。另外不锈钢的加工硬化趋势严重,工件表面易产生残余应力。
特别是在磨削细长轴类工件、薄壁工件等刚性较差的工件时,工件在磨削力的作用下很容易产生变形。
03.磨削不锈钢的砂轮选择
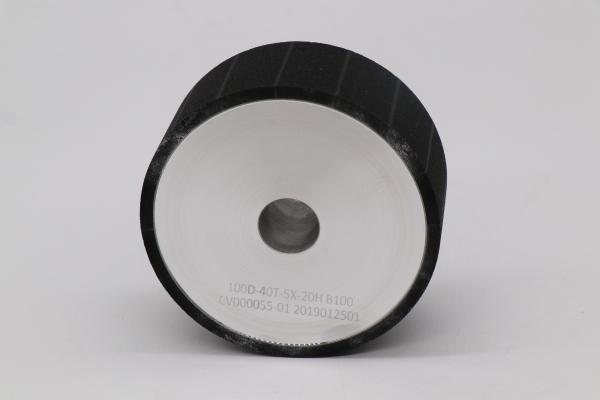
●磨料种类的选择
磨削不锈钢时,一般采用白刚玉(WA)。白刚玉具有良好的切削性能和自锐性。用立方氮化硼(CBN)砂轮磨削不锈钢效果最好(建议粒度F120,浓度100%,树脂结合剂)。由于CBN硬度高,磨粒不易磨损,化学稳定性好,与铁族元素无化学亲和力,磨削时不易堵塞CBN砂轮。
CBN砂轮磨削力小,磨削热低,不烧伤工件。但不锈钢用CBN砂轮价格比普通砂轮高,需根据实际情况修整。
单晶刚玉砂轮磨削效果仅次于CBN砂轮。因为每个磨粒都是球形多面体单晶,不存在机械破碎引起的裂纹和残余应力。如果单个磨粒的突然破碎较少,且硬度与韧性的匹配性好,则单晶刚玉具有良好的磨削性能。
磨削耐酸不锈钢时,可减少磨削划痕,特别是大孔径的单晶刚玉在生产中有良好的应用效果。
磨削Cr17Ni7A1沉淀硬化不锈钢时,采用微晶刚玉(MA)砂轮。微晶刚玉韧性大,切削性能好,使用寿命长,自锐性沿微晶的缝隙开裂,不会引起大粒或整个磨粒脱落,有利于减少磨削热和砂轮的堵塞。
磨削奥氏体不锈钢时,采用微晶刚玉与绿碳化硅制成的砂轮,可大大降低工件粗糙度,减少或消除烧伤。
●磨料粒度的选择
磨料粒度对表面粗糙度有直接影响。不锈钢韧性大,磨屑容易堵塞,如果使用细粒度的砂轮,磨料失去切削作用,工件表面光洁度不高。结果表明,粗磨时采用F36、F46粒度,精磨时采用F60粒度。粗磨和精磨时均采用F46、F60粒度砂轮。
●结合剂的选择
不锈钢具有韧性大、耐高温、强度高、磨削力大等特点,因此要求砂轮具有较高的强度,能承受较大的冲击载荷。
磨削不锈钢时,可用陶瓷结合剂砂轮,具有良好的防水、耐热、耐腐蚀性能,能保持良好的切削性能,生产效率高,缺点是脆性大,不能承受较大的冲击和弯曲。
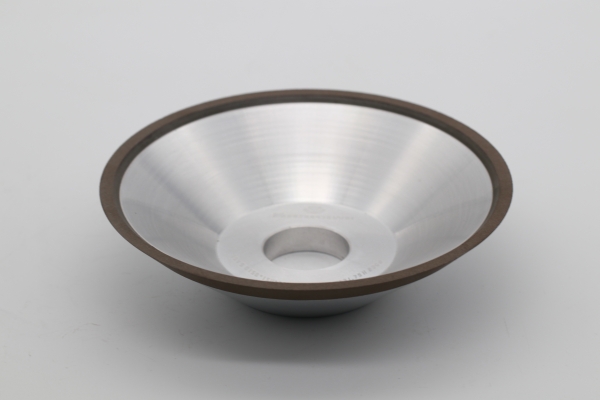
树脂结合剂砂轮用于不锈钢的切割、开槽、无心磨削,强度高、弹性好、抗冲击、孔隙多,可用于较高的圆周速度(35-75m/s)。但树脂结合剂砂轮硬度较低,将树脂砂轮放入石蜡中,可防止碱性溶液的影响。另外,当温度高于150℃时,树脂结合剂会软化,降低强度,甚至烧伤,因此磨削时应冷却。
●砂轮硬度的选择
磨削不锈钢时,应选用硬度较低的砂轮,砂轮自锐性较好。硬度过低,磨粒结合不牢,磨钝前脱落,将大大降低不锈钢砂轮的使用寿命。
总之,磨削不锈钢时,应根据经济情况和磨削材料的实际情况,选择CBN砂轮和普通砂轮。此外,实际应用中也有采用普通砂带、CBN砂带进行磨削的。
河南磨澳始终致力于研发和生产更先进的金刚石及CBN砂轮,以提供给客户完善的磨削解决方案!
用磨削创造比磨削更多的价值!!!