单晶刀具在精密加工领域的优势
在近现代,部分行业对机械化加工的要求越来越高,不仅需要加工快、稳、久更要求“微、小、精。机械加工方法中,用单晶金刚石刀具加工超精密工件主要有较高的硬度和耐磨性、有很好的导热性,较低的热膨胀系数、刃面粗糙度较小,刃口非常锋利、摩擦系数低,切削时不宜产生积屑瘤等优势。
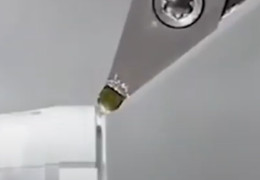
那么如此精密的单晶刀具是如何磨削的?
一 粗磨
磨澳可为单晶刀具的粗磨提供800#或1000#金属金刚石砂轮(适用于COBORN PG系列磨床)或陶瓷金刚石砂轮,两种砂轮各有优势。金属金刚石砂轮较之陶瓷金刚石砂轮有着更长的寿命和更好的保型性,粗磨后的精度更高;陶瓷金刚石砂轮则更为经济,更具性价比,同时陶瓷砂轮自锐性好,更容易修整,不失为一个好的选择。
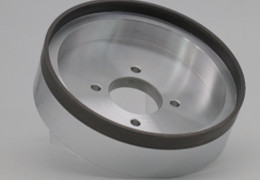
当然,近些年激光技术也取得了很大的进步,部分工厂也会选择使用激光进行粗磨(也可以算是切割),这也能在一定程度上提高生产效率,不过也需要注意激光过后单晶边缘是否出现发黑烧伤的情况。
二 精磨
到了精磨这一阶段,多选用金属金刚石砂轮和铸铁盘。金属金刚石砂轮进行精磨时使用粒度为6000#,磨澳目前最细粒度可做到10000#,磨削后可达到客户要求。如使用铸铁盘磨削,则需要在盘上加入金刚石粉,最终加工到所需要的精度。
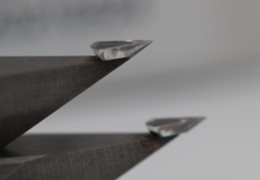
也有部分用户会选择用陶瓷金刚石砂轮精磨单晶刀,目前也取得了不错的反馈。同金属砂轮一样,陶瓷砂轮最细粒度也可达到10000#,磨削后刀具刃口可达3μm。
三 超精磨
铸铁盘可实现最后超精磨削工序。进行超精磨削时,需使用1μm或小于1μm的金刚石粉。磨削前,需将金刚石粉加入油或其它类似物质混合成研磨膏,涂敷在铸铁盘表面,放置一段时间使研磨膏充分渗入铸铁盘孔隙,再对表面进行预研磨,加强金刚石粉在铸铁盘孔隙中的镶嵌作用。完成此步骤后,方可对单晶刀具进行最后一道磨削。
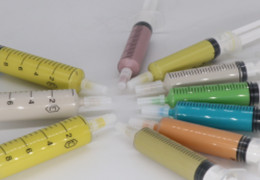
在具体磨削过程中有部分客户会遇到一些砂轮或金刚石粉粒度很细,但是却始终磨不到要求的情况。这可能主要有两方面原因:一是粗磨崩边过大,精磨修不回来;另外就是精磨混入大颗粒或者堵塞,导致工件划伤。
磨澳可长期提供具有更高稳定性的单晶刀砂轮,保证粗磨刃口质量,帮助您节省精磨时间和成本,提高精磨效率。